Each of the methods below of joining metals has its own advantages and characteristics.
Silver Brazing
Silver brazing requires high heat of around 1350° F and is very strong. It is fairly corrosion resistant, but will tarnish with age.
Silver brazing is sometimes called silver “soldering”, but that is bit of a misnomer, because soldering is a low temperature process. It is even more confusing, because another type of silver soldering involves the use of low-melting point Silver/Tin alloy. So let’s call silver brazing by its more descriptive name. Silver brazing is a high temperature process and somewhat time-consuming because of the time which may be required to heat up a part.
The joint area is well-fluxed with a borax paste that is able to clean oxides off the metals when it is molten while resisting boiling off in the flame for a short while. When the materials are up to almost dull-red, silver alloy wire is fed into the joint area. Over-heating can cause oxidation, which will keep the metals from being wetted by the solder and flux.
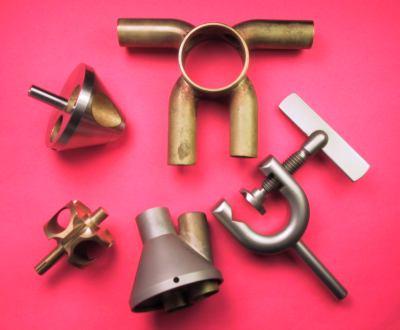
Small parts are easier to braze than large ones because of the heating time or total heat needed. A good deal of cleanup after brazing can be needed, including acid treatment of oxides and/or buffing of the assembly. Parts which are in a hard condition will be annealed by the process. Silver brazed brass parts can become fully annealed or distorted by the process. Silver brazing can create a very controlled joint, and its strength is certainly a factor in its favor.
Although silver brazing material is commonly an alloy with Cadmium it is not necessary to endure such a health risk. We use Cadmium-free filler wire. That has the added advantage of Cadmium’s being absent from the final joint to the customer.
For a musical instrument manufacturer, we developed ways of silver brazing together two half-sections of a trombone valve for a leak-free joint, and then made a brazing jig for holding four brass tubes in place for accurate location.
Soldering
There are two basic solder types we deal with, though there are others. Aluminum can be joined with a “solder” but here we are discussing Lead/Tin and Silver/Tin solders.
Soldering is a low temperature process, rarely above 425° F which is similar to brazing, but involves flux-wetting both parts and filling with a Lead/Tin or Silver/Tin wire or paste. It results in a low to medium strength joint which is fairly corrosion resistant. Designing a joint with enough metal-to-metal contact can minimize the strength problem.
Stainless tubing assemblies can be easily joined by this process, while not running the risk of annealing or softening them. Silver/Tin solder is becoming the preferred material for medical uses, because of the absence of lead, and because the joints remain fairly corrosion free.
Many metals can be soldered such as steel, brass, stainless and copper.
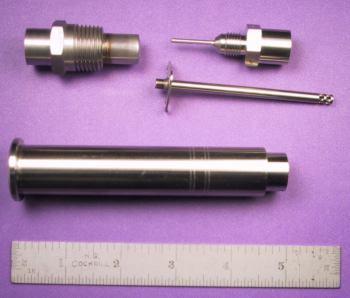
TIG Welding
TIG welding involves very high temperature melting of the metal itself with no filler required and is an excellent process for the strongest possible joint between stainless steel pieces, steel, or steel to stainless pieces, some bronzes, or copper to copper. After passivating stainless steel, the welded joint is about as resistant to corrosion as the parent metals. Often, passivation is not required.
Parts often have to be designed to fit the process so that filler is not needed. Enough material has to be available to melt together to form a good joint.
The electrode used to establish the arc to the work piece is made of Tungsten, like a light bulb filament. Electrodes we use are usually in the range of .025″ to .125″ in diameter. To keep the Tungsten electrode from burning up, a shield of gas, usually Argon, is used to provide an inert atmosphere. Thus the name of the process TIG, or Tungsten Inert Gas.
Although we do have manual capability with TIG which we use now and then, our main strength is in TIG welding on a special lathe.
This lathe is totally automated after the Start button is pushed. A shield of Argon is established around the electrode, the spindle starts to rotate, the high frequency arc starter is actuated, the arc is established, an arc of a pre-set time is continued around the work piece, an arc decay to eliminate “craters” takes over, and then the arc stops, while a bath of Argon plays on the piece, protecting the weld area and the electrode from excess oxidation. All of these steps above are adjustable.
We have had laser welding done for us on some larger pieces and discovered that weld penetration is difficult with lasers, so weld strength was mediocre. We get a higher strength joint with our lathe. Weld appearance can be exceptionally good and smooth since the process is automated.
This welding machine will also make accurate non-rotated welds, by simply turning the spindle rotate function off.
It is not advisable to use 303 stainless or hardenable alloys when TIG welding. The very characteristic of 303 stainless which makes the chip break up while machining, makes it crack when it is welded. Silver brazing or low termperature Silver-Tin soldering can be a better way to join 303 stainless parts. If using stainless alloys, use 304L or 316L which are low carbon variants of the standard alloys. They avoid weld cracking problems. Of course, 321 and 347 stainless are even better, but they are more expensive alternatives in material as well as labor.